In quest’ultimo decennio il termine “lean” è entrato finalmente a far parte anche del buon vocabolario dell’imprenditore Italiano.
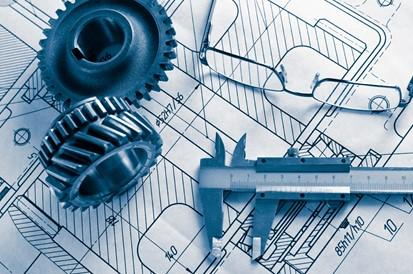
In Italia, come in Europa e negli stati Uniti, possiamo trovare corsi e convegni sull’argomento “lean thinking” oltre a numerose testimonianze che spiegano che cos’è, come si applica e quali risultati ha portato tra le aziende pioniere. Tuttavia, come spesso accade quando l’euforia generale prevarica l’effettiva conoscenza del metodo, quindi dei potenziali vantaggi e degli eventuali limiti, la sua applicazione rischia di ridursi a semplici approcci o ad una mera dichiarazione d’intenti.
Spesso si rischia di abusare degli acronimi perdendo di vista la sostanza nonché l’elemento indispensabile per il successo di ogni progetto di cambiamento: l’effettiva volontà di farlo da parte dell’imprenditore.
Procediamo tuttavia con ordine e precisiamo innanzitutto che il “pensiero snello” non nasce con Womack e Jones ma almeno 50 anni prima in Giappone.
All’origine del metodo ci sono, uomini come Taiichi Hono e Shigeo Shingo, ma soprattutto le migliaia di operai che lo hanno applicato e che devono essere considerati i veri fautori di quello che è stato poi denominato il Toyota Production System. Indiscusso merito dei due studiosi occidentali è stato quello di astrarre, da un approccio operativo fortemente contestualizzato all’interno di un settore (quello automobilistico), un sistema organizzativo-gestionale, concettualizando in una serie di principi applicabili a in ogni settore dove vi sia la necessità di organizzare e gestire fattori produttivi:
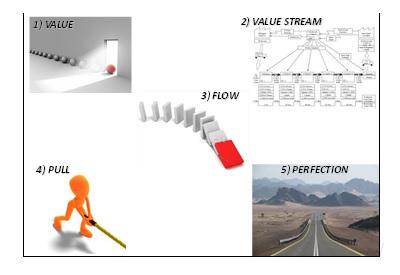
1) Value (Valore): Va definito il valore del prodotto o del servizio dal punto di vista del cliente finale: qual è il valore percepito dal cliente e quali attributi influiscono maggiormente.
2) Value Stream (Mappa il valore): Si devono identificare tutte le fasi necessarie, dall’acquisizione dell’ordine alla consegna finale, per ogni famiglia di prodotto: che relazione esiste tra le attività individuate e il valore percepito dal cliente. La singola attività contribuisce ad aumentare il valore per il cliente o è semplicemente il frutto di procedure errate, routine consolidate, complessità autogenerata dal sistema. Molte attività sono il frutto di come l’azienda è organizzata o di scelte pregresse su investimenti e tecnologie.
3) Flow (Flusso): Bisogna individuare le attività che effettivamente generano valore in flusso continuo senza interruzioni, al fine di ridurre drasticamente il lead time del processo. Il tempo è a tutti gli effetti un fattore produttivo e come tale il suo utilizzo deve essere improntato a criteri di efficienza ed efficacia.
4) Pull (Tirare): E’ necessario far tirare la produzione dal cliente. Dopo aver ridotto il lead time complessivo del processo ed eliminato le attività non a valore, allora non si dovrà più produrre su previsione ma si potrà utilizzare il mercato come schedulatore, fornendo al cliente ciò che vuole quando lo vuole.
5) Perfection (Perfezione): Il confronto deve avvenire direttamente con la perfezione e non con le aziende leader.
Negli anni 70, il mondo occidentale vide comparire sui propri mercati aziende nipponiche che mostravano di poter sostenere allo stesso tempo un vantaggio competitivo sia in termini di qualità che di prezzo, basti pensare all’arrivo di Honda, Yamaha, Sony, Toshiba, Panasonic, Nec, Fujitsu… e vi ricordate delle cassette TDK o Akai e degli Hi-Fi Aiwa?
La spiegazione più comoda fu, perlomeno all’inizio, di attribuire il gap esistente al sistema paese, ma successivamente una più attenta analisi ha permesso di distinguere i vantaggi competitivi effettivamente derivanti dalla “Japan Culture” ovvero:
- Bassa conflittualità sindacale (sindacalismo su base aziendale)
- Forte interazione tra sistema industriale e sistema bancario
- Profondo senso etico e sociale o del lavoratore giapponese
- Aumenti salariali basati sul criterio dell’anzianità
- Garanzia dell’impiego a vita per i lavoratori da quelli che, viceversa, erano i veri vantaggi competitivi derivanti da una diversa organizzazione del sistema aziendale e da un diverso approccio al modo di concepire, produrre e vendere il prodotto o servizio, ovvero:
> La necessità di far ripartire il mondo industriale con metodi semplici e a basso costo, rivolgendo gli investimenti sulla cultura delle persone e non prevalentemente sulla tecnologia
> La necessità di ridurre i “lead time” di produzione per produrre “ciò che serve quando serve”;
> La necessità di poter adattare con velocità i prodotti alle esigenze quotidiane ed alle sempre più frequenti
personalizzazioni, con una produzione a piccoli lotti orientata verso il “one piece flow”;
> La necessità di non creare scorte eccessive, per non appesantire liquidità aziendale, aumentare il cash flow e non ultimo occupare costosi spazi interni;
> La necessità di bilanciare la produzione per ottenere fluidità ed evitare “stress” alla struttura dovuti a code o sovrapproduzione, integrando i sistemi MRP con tecniche di chiamata “pull” e “visuale” di materiali e lavorazioni;
> La necessità di ridurre i costi “occulti” legati a ciò “che il cliente non è disposto più a pagare” gli errori, cioè i cosiddetti “muda” termine giapponese equivalente a “spreco” (vedi Fig 2);
> Le pressanti esigenze di recupero della produttività e marginalità aziendale per far fronte sia alle macro difficoltà di accesso al credito bancario (allora erano dovute al dopoguerra oggi alla crisi dei mercati finanziari), che come forma estrema di contrasto alle incertezze di solvibilità da parte dei clienti.
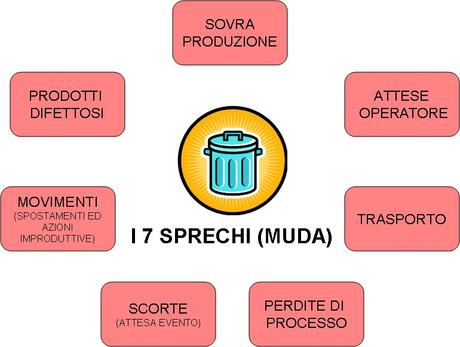
E’ su questo trascorso di circa 50 anni di esperienze tecniche e manageriali che siamo partiti per offrire oggi alla PMI Italiana di ogni settore un patrimonio di tecniche tipiche del TPS e di esperienza interessanti ed in grado di offrire reali miglioramenti delle performance.
Esse ovviamente vanno introdotte con giudizio e soprattutto declinandone i precetti in funzione del settore merceologico, ma le esperienze da noi vissute e le molteplici in atto, ne confermano la estrema attualità e validità con ritorni economici a volte impensati.
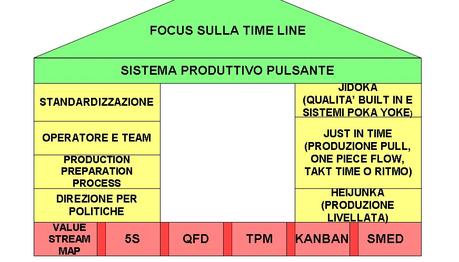
L’ approccio all’introduzione di tali tecniche sull’ Italian style
Ogni programma di miglioramento, e quindi anche quelli orientati alla produzione snella, deve partire dalla comprensione della storia e del “vissuto” aziendale, con un approccio olistico che non parli solo di strumenti e tecniche, ma che sappia inquadrare tutta l’azienda ( e le persone) verso un cammino di miglioramento.
Quello che i nostri consulenti descrivono come “l’Italian Style”, ovvero un concetto che non ha nulla a che vedere con il “Made in Italy”, ma che raccoglie una serie di prerogative con le quali non si può non confrontarsi prima, durante e dopo i progetti di cambiamento attuati nelle “nostre” PMI italiane.
Il sistema delle imprese italiane presenta aspetti per certi versi unici che ne impediscono l’assimilazione ad altre realtà:
- Peso estremamente elevato delle piccole e medie imprese sul P.I.L. e sul numero di imprese, soprattutto nelle attività industriali;
- Larga diffusione, tra le Pmi, di un modello di gestione familiare basato sull’azione diretta dell’imprenditore, affiancato da dirigenti solo in caso di dimensioni di un certo rilievo (coincidenza tra proprietà e controllo);
- Il modello industriale spesso è il frutto di un lungo e faticoso lavoro svolto quasi interamente dall’imprenditore che le ha create
- La cultura del cambiamento e del miglioramento in azienda è a volte molto “sopita” da prassi di gestione diretta e di accentramento delle responsabilità da parte dell’imprenditore.
“Fare la cosa giusta nel miglior modo possibile”
La comprensione degli obiettivi e soprattutto il forte impegno e condivisione della Direzione sono le leve fondamentali di ogni progetto, in funzione anche delle profonde trasformazioni al sistema (e spesso al lay out) che tali interventi richiedono.
Non si può pensare infatti ad introdurre il modello produttivo “lean oriented” senza avere la possibilità di produrre piccoli lotti; non si possono produrre piccoli lotti in modo economicamente conveniente senza ridurre il lead time del processo; non si può ridurre il lead time del processo senza prima ridurre i tempi di set-up dei macchinari; soprattutto non si possono condurre azioni di tale impatto senza una energica azione di management su obiettivi e risorse umane, conciliando ed allineando aspetti strategici e operativi.
Queste considerazioni ci aiutano continuamente ad affinare le tecniche per introdurre con efficacia i principi del “lean thinking” nelle PMI e ad oggi crediamo che un buon metodo possa essere quello caratterizzato da:
• Assessment iniziale, che evidenzi anche in forma economica i miglioramenti possibili, ivi inclusi i pay back degli investimenti e che sia “crudo” ma “sincero” negli esiti finali
• stesura di piani di miglioramento esaustivi, incentrati sul concreto raggiungimento degli obiettivi posti e con adeguati apporti di tempo e risorse. Per introdurre nuove tecniche in azienda non serve molto, ma per cambiare le persone occorrono sforzi e presenza costante
• approccio al lavoro in team, da parte nostra (sul campo operano team da 2 o 3 persone in relazione alla complessità dei progetti) ma soprattutto da parte dell’azienda (normalmente i team interni operano con 3 o 4 membri “chiave” dell’azienda) nell
• primi step di lavoro su aree “pilota” per evidenziarne da subito i miglioramenti di performance con alto rapporto “costi benefici”
• priorità ad interventi con logiche “low cost”, per convincere gradualmente e senza grandi investimenti economici l’imprenditore e per permettere al personale aziendale di rendersi conto da subito dell’efficacia dei risultati delle soluzioni introdotte
• creazione di dettagliati piani industriali, che possano descrivere i modi, i tempi e il rapporto costo investimenti/benefici derivanti derivati dall’introduzione delle tecniche, ma soprattutto che possano dare una visione completa del progetto all’imprenditore, dandogli la possibilità di focalizzare mentalmente un vero e proprio “piano di ammortamento”
• supporto diretto dei nostri team durante la delicata ed intensa fase operativa, con presenze costanti in azienda mirate sia al supporto tecnico dei vari membri dei team aziendali, che durante i vari incontri con i fornitori che praticamente sempre si rendono necessari
• sostegno al cambiamento, durante e dopo l’effettivo “go live” del progetto industriale in quanto la filosofia lean insegna che per seguire la strada che porta al miglioramento continuo, occorre qualcuno (i Sensei) che periodicamente ne ricordi la direzione, in quanto i pericoli di disastrose “marce indietro” sono spesso dietro l’angolo
• creazione della filosofia del miglioramento continuo, fatto di costante progettazione ed implementazione di progetti orientati al miglioramento e progressivamente rivolti ai livelli più operativi delle aziende, in quanto spesso è da li che possono arrivare i risultati più grandi. Raggiunto un risultato è necessario concentrare gli stimoli delle persone verso nuove mete per non far scendere la “tensione positiva verso i risultati”
• l’uso di sistemi incentivanti verso le persone, terminata la prima fase di sgrossatura industriale, crediamo che l’apporto positivo delle persone debba essere gratificato (anche economicamente) attraverso l’introduzione di sistemi che accomunino il risultato aziendale (efficienza e margine) con la soddisfazione economica personale (premi di produzione)
Per apprfondimenti, contattate il nostro esperto Rossano Storti