Quando si tratta di un elevato rapporto resistenza-peso, il titanio è proprio il miglior materiale disponibile per la produzione di telai per biciclette. Purtroppo, questi telai sono anche piuttosto costosi. Essi potrebbero presto scendere di prezzo, tuttavia: due società britanniche recentemente hanno unito le forze per creare il primo telaio da bici in titanio stampato in 3D al mondo.
Renishaw, una società di produzione di additivi, ha unito le forze con la Empyre Cycles per costruire la mountain bike monolitica in titanio MX-6 Evo. Empire offre una versione in alluminio già in produzione della MX-6.
Il telaio è stato costruito utilizzando una macchina di fusione laser AM250 prodotta da Renishaw. Nel processo di generazione, un laser ad alta potenza ad itterbio, con guida in fibra, è stato usato per fondere insieme selettivamente particelle di una polvere di lega di titanio. Strati di tali particelle fuse insieme sono stati costruiti l'uno sull'altro, per formare le sezioni finite del telaio. Tali sezioni sono state quindi unite insieme utilizzando un adesivo.
I componenti della staffa reggisella sono stati stampati insieme su una unica piattaforma di costruzione
Poiché il titanio ha una densità superiore a quella dell'alluminio, meno di esso doveva essere usato se Empire voleva una bicicletta finita che fosse più leggera del modello base. Per realizzare questo obiettivo, è stato usato un software di ottimizzazione topologica - questo valuta strutturalmente i modelli computerizzati di ogni parte del telaio e determina dove poter utilizzare meno materiale senza influire negativamente sulla resistenza.
Di conseguenza, per un totale di 1.400 grammi, il telaio Evo finito pesa il 33 percento in meno rispetto al suo omologo di alluminio. Quando il suo supporto reggisella è stato testato, ha superato la norma EN 14766 di resistenza per le mountain bike di sei volte. La resistenza del telaio nel suo complesso è ancora in fase di test.
Così, come potrebbe questo progetto portare a più convenienti telai in titanio? Per prima cosa, nel processo di fusione laser, non c'è spreco: tutta la polvere di lega di titanio che non è fusa per fare un telaio può essere riutilizzata in un altro, inoltre il processo di ottimizzazione topologica assicura per prima cosa di usarne il meno possibile. Inoltre, nessuna lavorazione particolare deve essere creata o impostata per progetti specifici di telaio, che sarebbe necessaria in caso di metallo fuso.
Dovrebbe anche essere relativamente semplice modificare i disegni del telaio se necessario, o per aggiungere caratteristiche personalizzate ai singoli telai. E, infine, non dovrebbe essere più difficile creare componenti con forme complesse rispetto a quelle relativamente semplici.
La Defence and Space Company European Aeronautic (EADS) ha già creato un telaio di bicicletta stampato in 3D, anche se è stato fatto in nylon.
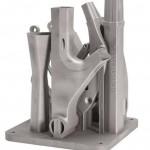
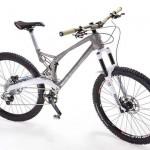